Ubicada en las colinas y caminos rurales de East Canton, Ohio, se encuentra una empresa que se enorgullece de estar a la vanguardia de la perforación sin zanjas: Barbco.
Su fundador, James S. Barbera, desarrolló algunas de las primeras tecnologías del campo, que él, su familia y un número creciente de empleados han suministrado a clientes nacionales e internacionales desde 1989. Es el tipo de empresa en la que los copropietarios y hermanos, James A. (gerente general), David (presidente) y Tony (CEO) Barbera trabajan en el taller de máquinas y la planta junto con sus empleados, sin importar el turno.
Contenido destacado
También es el tipo de empresa que reconoce una mejora de cambio de paradigma cuando la ve, con Barbco invirtiendo en mecanizado “monolítico” de cinco ejes (un gran componente de una sola pieza) después de descubrir que este método de fabricación podría reducir los tiempos de ciclo y aumentar durabilidad en varios productos exclusivos.
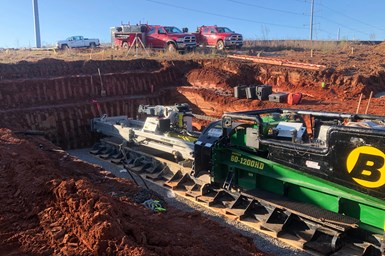
En su forma más poderosa, las máquinas perforadoras de Barbco pueden proporcionar más de un millón de libras de empuje y cientos de miles de libras-pie de torque. La compañía también proporciona herramientas, incluida su propia línea FlexBor, diseñada para capturar materiales y fluidos del proceso de perforación y evitar que se filtren al entorno circundante como “contaminantes” y “devoluciones involuntarias”. Foto cortesía Brent Scarbrough & Co., Inc.
La perforación sin zanjas se refiere al tipo de perforación subterránea que las empresas de servicios públicos o de petróleo y gas necesitan llevar a cabo. Mientras que la lógica tradicional exige cavar una gran zanja para tender tuberías, la tecnología de Barbco permite que los equipos de construcción avancen bajo tierra sin perturbar la tierra o la infraestructura de arriba.
Al hacerlo, las cuadrillas pueden diseñar hasta 60 pies de riel de vía para apoyar la instalación de la tubería del producto. La cuadrilla también necesita empujar la carcasa de acero consumible hacia el suelo para mejorar la estabilidad del túnel perforado, con ciertos sitios de trabajo, como los que están debajo de un ferrocarril, que requieren un cuidado especial para evitar que se asienten. Como tal, los productos de Barbco deben ser lo suficientemente flexibles y duraderos para manejar múltiples tipos de condiciones adversas.
Con su antiguo sistema de soldadura, Barbco “unía” tres piezas de riel que, debido a las fuerzas de arqueamiento únicas durante la soldadura, se volverían incompatibles con cualquier otra pieza de riel de vía. El CEO Tony Barbera llegó a decir que Barbco funcionaba “como un taller de autos deportivos”, ya que sus partes se convertían esencialmente en piezas únicas.
Maquinado de cinco ejes para manufactura monolítica
Durante muchos años, Barbco mecanizó y soldó piezas más pequeñas para fabricar sus piezas de mayor tamaño, pero la repetibilidad era baja y los tiempos de ciclo eran largos.
Las cosas comenzaron a cambiar en 2015, cuando la EPA revisó sus pautas para los motores diésel de nivel 3 y nivel 4, como los que se usan en la industria de perforación sin zanjas.
“Fue un verdadero desafío para nosotros porque todo tenía que hacerse mucho más grande”, dice Brandon Barbera, ingeniero de Barbco. Con un rediseño completo sobre la mesa, Barbco decidió dar el paso ambicioso de cambiar sus métodos de producción, con un enfoque final en la construcción de una sola pieza a través del maquinado en cinco ejes.
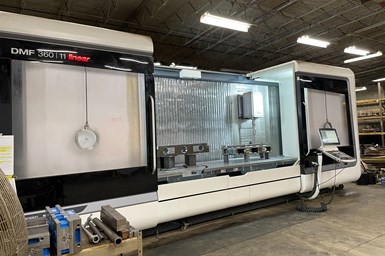
La flexibilidad para manejar piezas y cortes difíciles hace que la máquina de cinco ejes de Barbco tenga una gran demanda. La empresa compró centros de mecanizado CNC adicionales más pequeños para manejar piezas pequeñas y garantizar que la máquina de cinco ejes solo se use en el trabajo correcto.
Aunque la empresa comenzó de forma secuencial con la construcción de una pieza, específicamente, adaptadores macho con forma hexagonal, su primera compra de cinco ejes fue una máquina grande: una DMG MORI DMF 360|11 lineal de cinco ejes. Barbco también compró una torno-fresadora DMG MORI y ha utilizado esta combinación para iniciar un camino inusual, pero que ha traído un gran éxito: la consolidación del ensamblaje para piezas monolíticas.
Hasta ahora, Barbco ha consolidado tres partes: una barra de empuje, un rodillo de gancho y el riel de la vía. La máquina de cinco ejes mejoró el acceso a las piezas, lo que le permitió a Barbco mecanizar estos componentes en una sola pieza (en su mayoría), incluir nuevas operaciones, fortalecerlas con materiales más baratos y lograr una mayor repetibilidad.
Soldadura de la vieja escuela
Con su antiguo sistema de soldadura, Barbco “unía” tres piezas de riel que, debido a las fuerzas de arqueamiento inconsistentes durante la soldadura, se volverían incompatibles con cualquier otra pieza de riel. El CEO Tony Barbera llegó a decir que Barbco funcionaba “como un taller de autos deportivos”, ya que sus partes se convirtieron esencialmente en piezas únicas. El etiquetado de partes de pistas que iban juntas ayudó, pero estaba lejos de ser una solución ideal para los clientes que necesitaban pistas más largas.
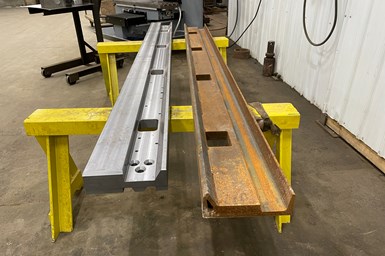
Los diferentes métodos de producción de Barbco dan como resultado distintos diseños. La pieza monolítica de la izquierda es el nuevo riel de vía de Barbco, que se fabrica mediante mecanizado en cinco ejes. Debido a las limitaciones de capacidad, Barbco ha continuado soldando algunos rieles, incluso mientras gira hacia el mecanizado de cinco ejes.
Las conexiones entre las secciones de la pista requerían que Barbco enviara “escudetes” sueltos que los clientes usaban para alinear físicamente la pista antes de soldar el refuerzo en su lugar. Piezas como la barra de empuje, que encaja en los orificios de la pista para proporcionar una base de empuje al mover la máquina perforadora, también requerirían varios tipos de acero para satisfacer las necesidades de resistencia de las diferentes secciones de la pieza, lo que aumentaría los costos. Es posible que las versiones soldadas de la barra de empuje y el rodillo de gancho no tuvieran los mismos problemas de “barra caliente” que el riel, pero aun así requerían procesos de ensamblaje complicados. Solo la barra de empuje precisaba 12 piezas, algunas de las cuales debían atornillarse al cuerpo principal.
Si bien el taller de máquinas en sí ha experimentado un crecimiento a gran escala para mantenerse al día con el aumento de trabajo, el departamento de fabricación ha visto cambios en el enfoque del proyecto en lugar de cambios en el personal. Los cabezales de corte de las máquinas de Barbco, por ejemplo, todavía dependen de la soldadura, y con más empleados de fabricación trabajando en ellos, el taller puede entregar los envíos más rápido.
Pasando al mecanizado
Estos problemas han desaparecido en gran medida con el mecanizado CNC. Además de las grandes máquinas DMG MORI, Barbco utiliza dos centros de mecanizado CNC estilo Bridgeport más pequeños, y sus dos máquinas CNC más antiguas, para manejar piezas más pequeñas que se benefician del fresado.
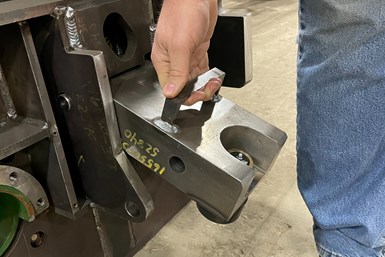
Los rodillos de gancho de Barbco están ubicados en las esquinas de las unidades de empuje de la base. Estos rodillos soportan y anclan las máquinas perforadoras de la empresa a los rieles. La construcción de cinco ejes aún requiere ensamblaje para unir el mango al cuerpo principal, pero es mucho más fuerte que la pieza soldada original.
La consolidación del ensamblaje, que reforzó el rodillo de gancho, aumentó el peso de la pieza, ahora sólida. Por razones prácticas, su mango aún debe fabricarse con una pieza de metal diferente y unirse como una segunda pieza, pero en general, los operarios de Barbco informan que la pieza es mucho más fácil de fabricar mediante el mecanizado de cinco ejes.
Las 12 partes de la barra de empuje en el diseño de soldadura se redujeron a una parte con el diseño CNC de cinco ejes. En lugar de laminar acero A36 con acero A514, el taller puede usar exclusivamente acero A36. Las barras de empuje de 7 pulgadas de espesor para las máquinas de 36 y 48 pulgadas pueden usar el mismo bloque, lo que simplifica aún más la cadena de suministro de Barbco, mientras que las barras de empuje de 8 pulgadas de espesor para las máquinas de 60 pulgadas usan un bloque con más acero.
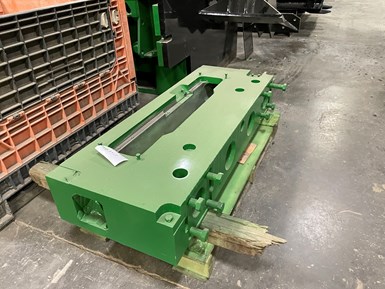
Las barras de empuje de Barbco se mecanizan a partir de un bloque en el nuevo sistema de producción. Estos dispositivos se colocan debajo de las máquinas perforadoras de Barbco y conectan estaciones (llamadas “agujeros para perros”) en la pista con el fin de proporcionar una base de empuje para el movimiento de la máquina.
Al generar menos calor que la soldadura, el mecanizado de cinco ejes también ha mejorado la repetibilidad de los juegos de rieles de 34 pies. Como resultado, los usuarios ya no necesitan conectores especializados para combinar los rieles.
El departamento de fabricación y el taller de operarios se han sometido a importantes revisiones debido a este cambio de proceso. Si bien el taller de máquinas ha crecido para mantenerse al día con el aumento del trabajo, el departamento de fabricación ha visto cambios en el enfoque del proyecto en lugar de cambios en la dotación de personal. Los cabezales de corte de las máquinas de Barbco, por ejemplo, todavía dependen de la soldadura, y con más empleados de fabricación trabajando en ellos, el taller puede entregar los envíos más rápido. Tom Schmidt, vicepresidente de desarrollo comercial, estima que este cambio ha permitido a la empresa casi duplicar sus ventas de cabezales de corte en 2021.
Los departamentos de fabricación y mecanizado, que ahora colaboran regularmente en el desarrollo de piezas, investigan qué otras piezas podrían beneficiarse de la consolidación del ensamblaje y el mecanizado de cinco ejes, y luego equilibran estos beneficios con la practicidad del mecanizado y otras consideraciones. Por ejemplo, mecanizar la pieza en bruto de un cabezal de disco en una sola pieza mejoraría el rendimiento, pero los canales en la cara de la pieza dificultarían mucho el mecanizado.
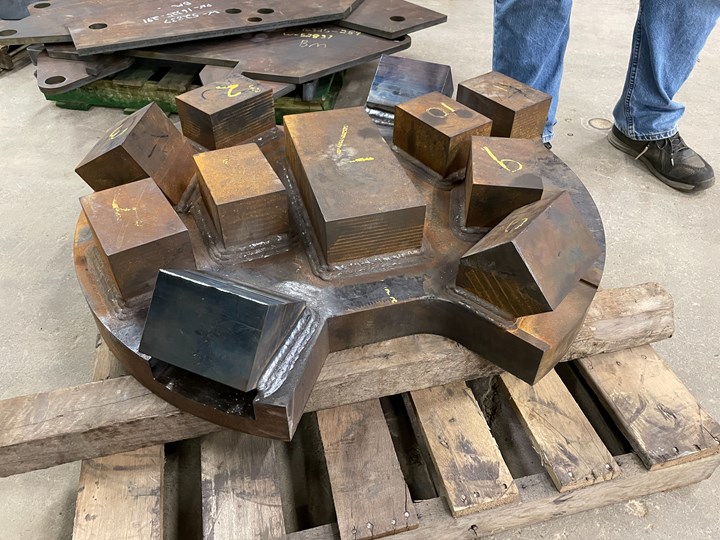
Los equipos de fabricación y taller de mecanizado de Barbco discutieron si una pieza en bruto con cabezal de disco sería candidata digna para la consolidación del ensamblaje a través del mecanizado de cinco ejes. Infortunadamente, los canales profundos de la pieza causarían dificultades significativas.
Optimización de herramientas de corte y software
El cambio de un ciclo de producción basado en piezas soldadas, a un ciclo de producción basado en fresas escariadoras de alto avance generó una revisión completa de las herramientas de Barbco.
Cuando la empresa daba sus primeros pasos en el mecanizado de cinco ejes, desafió a los representantes de varias empresas de herramientas para que entregaran herramientas que cumplieran con los requisitos de rendimiento. El programador de Barbco, Michael Craig, recordó un caso en el que trabajó con un representante de herramientas en el taller para optimizar una herramienta. Después de algunas pruebas y errores con las velocidades y diversas llamadas telefónicas, la herramienta pudo completar un corte 45 minutos más rápido que su predecesor.
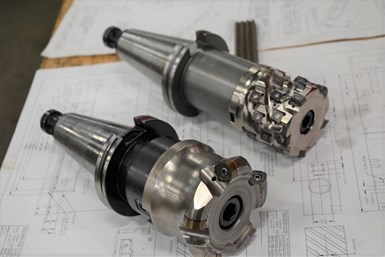
Las nuevas herramientas octogonales de Barbco condujeron a un fuerte aumento en la productividad, al tiempo que extendieron la vida útil del carburo. Con él, Barbco puede usar el DMF 360|11 para mecanizar un conjunto de rieles en tres turnos, una mejora de productividad del 33 % con respecto a las herramientas anteriores. Foto cortesía John Barbera, 360 Social Solutions.
Para un ejemplo específico de cambio de herramientas, Barbco cambió su fresa de cara cuadrada de 4 pulgadas de diámetro por una herramienta de fresado de alto avance octogonal de Mitsubishi. Esta herramienta puede funcionar a una velocidad de avance más alta con virutas más grandes. Los puntos de corte adicionales distribuyen la fuerza, y los insertos de carburo duran para dos o tres conjuntos de rieles, a diferencia de solo uno que se lograba con la herramienta anterior. Como resultado, la cantidad de turnos necesarios para mecanizar un conjunto de rieles se redujo de 4,5 a 3.
Los cambios de herramientas también han llevado a cambios de diseño. Por ejemplo, el riel originalmente incluía un canal de 3,875 pulgadas mecanizado en dos pasadas. Después de que un operario sugiriera usar una herramienta de 4 pulgadas y simplemente ampliar el canal, el equipo modificó la pieza y completó con éxito la operación en una sola pasada.
El supervisor asistente Andrew Liston dice que el Mastercam hace más fácil “trabajar con una herramienta en lugar de tener que cambiar las herramientas”. Craig apunta a la programación que permite mecanizar paredes rectas y desbastar ángulos de esquina en una sola operación, lo que antes requería operaciones separadas con varias herramientas.
Los cambios en el software CNC y CAD han llevado a más revisiones en los diseños y procesos de Barbco. El CNC de cinco ejes de Barbco ha permitido que el taller agregue funciones como “placas de guía”, que hacen conexiones más fuertes entre las piezas que los refuerzos y, al mismo tiempo, aumentan la durabilidad. La implementación del Mastercam a mediados de 2020 simplificó y estandarizó la programación en el taller de máquinas.
El supervisor asistente Andrew Liston dice que el Mastercam hace más fácil “trabajar con una herramienta en lugar de tener que cambiar las herramientas”. Craig apunta a la programación que permite mecanizar paredes rectas y desbastar ángulos de esquina en una sola operación, lo que antes requería operaciones separadas con varias herramientas.
Barbco también aprovecha la función de fresado dinámico de Mastercam. Craig dice que esta capacidad “nos permite usar una profundidad completa” mientras mantiene el desgaste de las fresas lo suficientemente bajo como para usar una herramienta para múltiples rieles.
Incluso los cambios más pequeños, como mover las tolvas de virutas, han afectado los tiempos de ciclo; los operarios de Barbco se han dado cuenta y buscan nuevas formas de optimizar continuamente la producción.
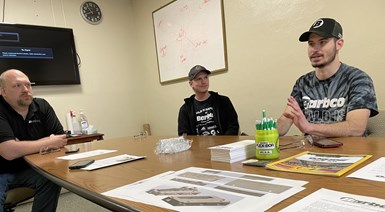
El supervisor asistente del taller de máquinas, Andrew Liston (centro), el programador Michael Craig (derecha) y otros maquinistas pueden disfrutar de competencias amistosas de productividad bajo la atenta mirada del gerente del taller de máquinas Matt Wolf (izquierda), pero al final del día todos siguen siendo parte de la cultura de beneficio común y colaborativa que el vicepresidente de desarrollo comercial, Tom Schmidt, llama el corazón del “orgullo” de Barbco, como en una manada de leones.
Resolviendo problemas crónicos
La producción de Barbco es más rápida, más precisa y económica con la producción de cinco ejes, pero quedan dos desafíos familiares: los límites de capacidad y de personal.
Si bien el taller de maquinaria y el departamento de fabricación de la empresa son más grandes que nunca, y Schmidt dice que las ventas internacionales le han permitido a la empresa evitar despidos durante los meses de invierno históricamente escasos, Barbco aún no ha podido cubrir todos sus puestos. Como tal, ha estado atenta a las nuevas estrategias de contratación y retención, incluida la formación de asociaciones regionales.
En marzo de 2021, Barbco ayudó a fundar la Asociación para el Desarrollo del Trabajo de Manufactura del Condado de Stark (SCMWDP, por sus siglas en inglés). Esta organización se acerca a los estudiantes, educadores, y socios de la comunidad como OhioMeansJobs y la Liga Urbana del Condado de Greater Stark para cambiar las percepciones sobre la fabricación y buscar talentos de entornos no asociados tradicionalmente con el campo.
También fomenta el intercambio de conocimientos entre los fabricantes del condado de Stark y las empresas de otras organizaciones miembros de la Asociación de Fabricantes de Ohio. Barbco se ha hecho cargo de este esfuerzo y se ha asociado con la Universidad de Walsh para desarrollar un programa de análisis de datos que la empresa espera que mejore las habilidades de sus empleados.
Sin embargo, en términos de capacidad, los pedidos acumulados con trabajo para entre seis y ocho meses de la compañía es más corto que el trabajo acumulado con el modelo de soldadura, pero aún no es ideal.
Barbco compró algunos centros de mecanizado horizontal de segunda mano para desbastar y taladrar piezas antes de colocarlas en la DMF 360|11, que luego solo necesitaría realizar trabajos de fresado de acabado y trabajos específicos de cinco ejes, pero la empresa todavía está maximizando la capacidad de la máquina. Ni siquiera pasar a un sistema de tres turnos en julio de 2021 con el fin de operar las 24 horas ha demostrado ser suficiente para satisfacer la demanda.
En última instancia, la solución de Barbco podría ser mantener el rumbo: la empresa planea seguir su inversión en nuevos centros de mecanizado CNC cada 12 meses.
CONTENIDO RELACIONADO
-
Para qué sirve el fresado en duro
El fresado en duro se utiliza para mecanizar aceros endurecidos con filos cortantes definidos. El fresado de estos materiales requiere centros de mecanizado de alta velocidad configurados para el fresado en duro, junto con un CAD/CAM programado en concordancia.
-
¿Cuál es el centro de mecanizado de cinco ejes adecuado para su taller?
Con tantas opciones en tecnología de mecanizado de 5 ejes, ¿cómo saber cuál es la mejor para su taller? Primero, considere las partes. Luego, observe los procesos existentes y los beneficios potenciales del maquinado en cinco ejes.
-
Análisis de modo de falla y efectos (FMEA) en un taller de mecanizado
El nuevo estándar ISO 9001:2015 enfatiza en la evaluación de riesgo. Los talleres médicos como Protomatic, con certificación ISO 13485, ya lo están gestionando con el análisis de modo de falla y efectos (FMEA).