“Cortamos antes de cortar”. Ryan Patry no pretendía ser misterioso cuando dijo esto. Patry es un reconocido experto en la materia de fabricación de Lockheed Martin en Sikorsky, una empresa de Lockheed Martin. “Cortamos antes de cortar” describe acertadamente la metodología de fabricación avanzada que la empresa desarrolla e implementa en una fábrica digital de Stratford, Connecticut.
Una celda de mecanizado en pleno funcionamiento incorpora muchos de los principios más importantes del concepto de fábrica digital de Sikorsky. La celda comenzó a realizar su proceso de corte en julio de 2020, unos seis meses después de la instalación de las máquinas, pero en cierto sentido, estaba mecanizando antes de eso. Todos los elementos del proceso, desde los componentes estructurales de la máquina y la cinemática hasta las complejidades de los conjuntos de herramientas de corte y los dispositivos de sujeción, ya se habían duplicado en el ámbito virtual como modelos digitales.
Contenido destacado
“Dado que estos modelos digitales eran sustitutos exactos del equipo real, podían usarse para simular todos los procesos de mecanizado como gemelos digitales”, explica Patry.
Debido a que Patry y su equipo confiaban en que los resultados virtuales de las simulaciones serían indistinguibles de los resultados reales, la celda podría comenzar las operaciones de desbaste inmediatamente después de completar el periodo de prueba de la celda.
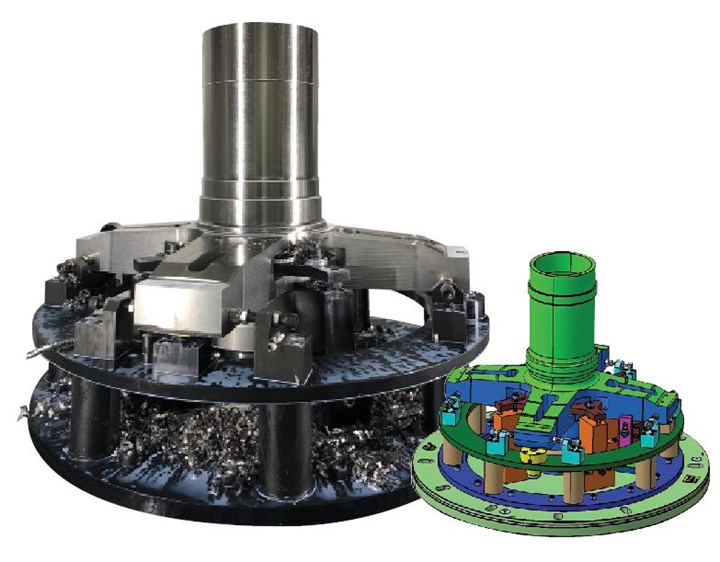
Un gemelo digital del cubo del rotor y su fijación puede ser una ayuda para el personal que replica la configuración en el mundo real. Los gemelos digitales también impulsan las simulaciones que establecen objetivos geométricos para cada fase del mecanizado. Las trayectorias de las herramientas evitan intencionalmente partes de diseños que aún están en desarrollo.
Las dos primeras piezas de trabajo que surgieron de la celda fueron un cubo de rotor de titanio y una carcasa de caja reductora de aluminio para el Raider X, de Sikorsky, prototipo de helicóptero que es uno de los dos únicos contendientes restantes en una competencia por un contrato del ejército de Estados Unidos. Como era de esperar, la comparación de los datos de inspección de la pieza de trabajo con los modelos digitales confirmó que los resultados reales del mecanizado no se diferenciaban de los obtenidos en la simulación.
La importancia de este logro no se puede subestimar, dice Pete Germanowski, ingeniero jefe del Raider X. Como la oferta de la compañía para el programa Future Attack Reconnaissance Aircraft (FARA), que es parte del esfuerzo Future Vertical Lift del ejército de Estados Unidos para revolucionar su flota, el Raider X representa un cambio transformador en la aviación militar, explica. Era un hecho que cumplir con las expectativas también requeriría un paso radical en la capacidad de fabricación.
“Como licitador competitivo en el programa FARA, tenía objetivos estrictos de asequibilidad, producibilidad, cronograma y confiabilidad que cumplir”.
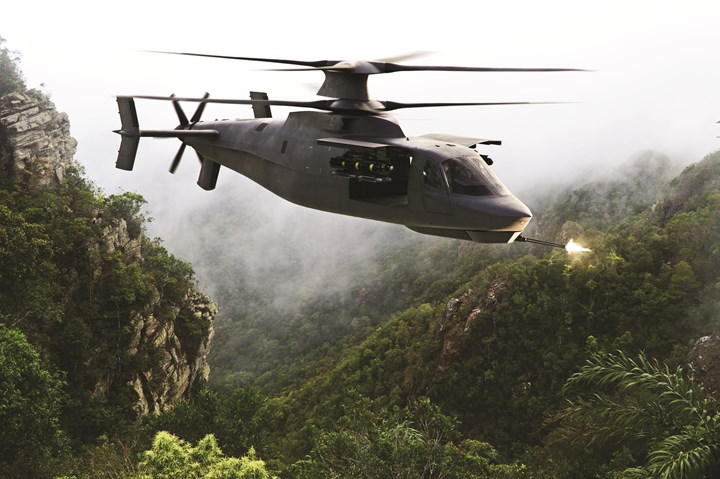
El Raider X tiene una velocidad máxima de más de 290 mph y un alcance de 400 millas. Propulsado por el motor de turbina de reacción T901, de GE Aviation, con una potencia nominal actual de 3,000 hp en el eje del rotor, la aeronave puede ascender a 9,000 pies.
La aviación avanzada se encuentra con la manufactura avanzada
Diseñado para volar bajo y rápido sobre el terreno con el fin de evitar ser detectado, el Raider X es un helicóptero coaxial compuesto (CCH). Este diseño se caracteriza por dos conjuntos de rotores montados uno encima del otro en el mismo eje vertical, que giran en direcciones opuestas. Los rotores coaxiales agregan estabilidad y maniobrabilidad, y superan la tendencia de un solo conjunto de rotores a perder sustentación a altas velocidades.
Otra característica destacada del Raider X es el propulsor orientado hacia atrás, que reemplaza el propulsor de cola montado lateralmente, de un helicóptero convencional. Este diseño de hélice de empuje ayuda a los pilotos a acelerar o reducir la velocidad sin hundir ni levantar la nariz.
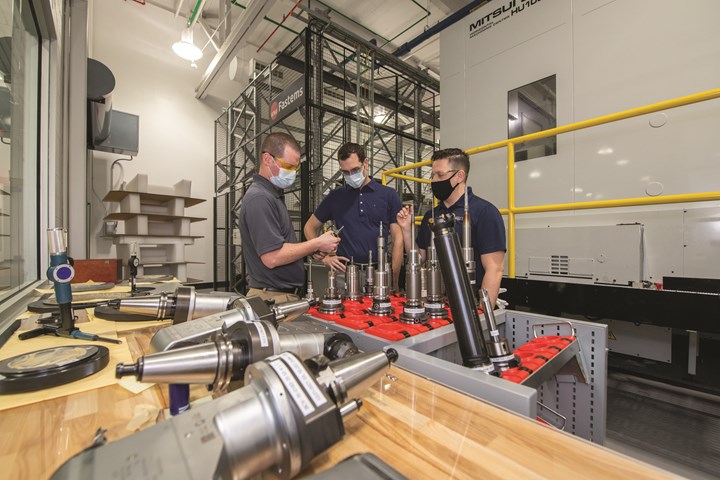
De izquierda a derecha, Ryan Patry, ingeniero de fabricación; Pete Germanowski, ingeniero jefe, y Jason Pratts, ingeniero de fabricación, revisan las herramientas de corte en la celda de mecanizado.
Estos adelantos en la aviación se vinculan directamente con la tecnología avanzada en la celda de mecanizado, que produce ocho piezas únicas para el rotor principal, el motor propulsor y la caja reductora principal.
Por ejemplo, los dos tornos verticales Fives Giddings & Lewis VTC 2500, idénticos, son apreciados por su capacidad para acomodar un cabezal de fresado motorizado, que permite sincronizar orificios y ranuras para el ensamblaje del eje principal en la misma operación de montaje de las operaciones de torneado.
“La precisión obtenida al combinar estas operaciones es esencial en el rendimiento de un helicóptero coaxial, porque la sincronización de la rotación de los rotores es la clave para un vuelo estable y un vuelo estacionario preciso de la aeronave”, explica Patry.
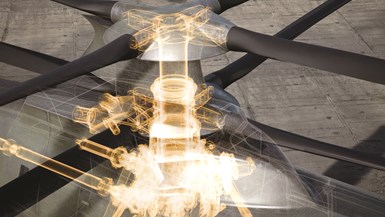
Ryan Patry, de Sikorsky, define un gemelo digital como la representación actual de un producto en forma digital aumentada con los datos de diseño/construcción mantenidos a lo largo del ciclo de vida de un producto.
Las otras dos máquinas de la celda, los HMC gemelos Mitsui Seiki HU 100-A-5X, ofrecen el torque, la rigidez y la precisión para cortar titanio de manera efectiva, incluso en operaciones simultáneas de cinco ejes. La celda, que ocupa 36,259 pies cuadrados dedicados y con clima controlado, también incluye sistemas de pallets para cada VTL y un FMS para los dos HMC, que permite operar las 24 horas del día en tres turnos. Sin embargo, la “historia real” no es el equipo, sino “las características operativas de la celda”, dice Patry. De hecho, lo llama un “microcosmos” de la capacidad de fabricación digital general necesaria para fabricar el Raider X.
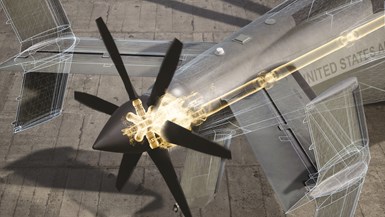
Un beneficio del gemelo digital es la visualización de ensamblajes complejos, como este tren de transmisión del rotor propulsor o el ensamblaje del rotor principal que se muestra arriba.
Por ejemplo, los ingenieros emplearon ampliamente la simulación 3D para probar y luego modificar los diseños en función de los aportes de los técnicos familiarizados con la construcción, el mantenimiento y el vuelo de helicópteros.
Como resultado, el helicóptero no solo tiene una gran capacidad de vuelo, sino que también es fácil de montar, reparar y actualizar. En la celda de mecanizado, los mismos conceptos esenciales permiten reducir los plazos de entrega mediante la producción de componentes aptos para el aire sin cortar primero las piezas de prueba reales.
“Comenzamos a desbastar las piezas, incluso cuando aún se estaban trabajando los detalles del diseño final, por lo que las piezas se producen mucho más rápido que en cualquier programa de desarrollo anterior”, dice Patry.
La celda de maquinado en funcionamiento
Un observador en el taller probablemente no notaría nada diferente sobre el proceso de corte de metal en sí. La salpicadura de refrigerante y las virutas que golpean la carcasa de chapa parecería bastante normal para máquinas tan grandes y poderosas. Al menos en la superficie, las operaciones parecerían seguir la secuencia típica de tres fases de desbaste, semiacabado y acabado.
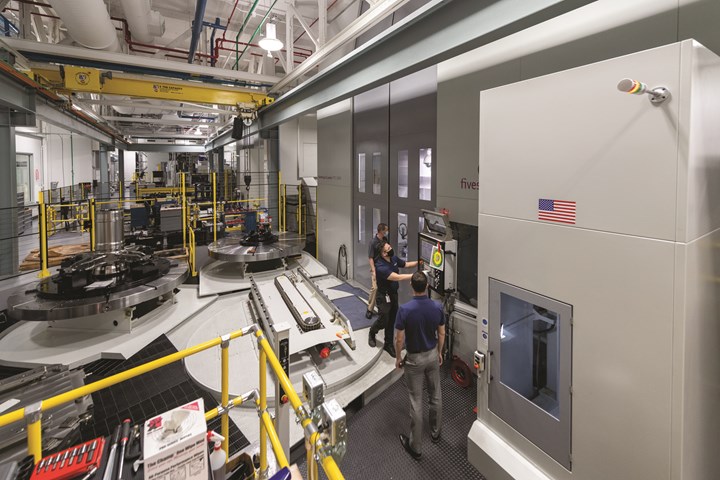
Este VTC es atendido por un cambiador de pallets automatizado. Un segundo VTC idéntico en la celda está equipado de manera similar. Ambos cuentan con mesas de 2,500 mm (98.4 pulg.), volteo máximo de torneado de 1,560 mm (61.4 pulg.) y 1,750 mm (68.9 pulg.) de recorrido vertical en el eje Z, así como un pistón hidrostático para rigidez y eje X que se desplaza hacia la izquierda y hacia la derecha del centro para cortar (o sondear) desde cualquier lado..
Sin embargo, el observador puede sorprenderse al notar que cada operación de mecanizado va seguida de una inspección sin contacto para generar un modelo 3D de la pieza de trabajo. Esto es necesario porque el mecanizado se rige por otro modelo 3D derivado, no del escaneo de una pieza, sino de simulaciones anteriores de esa fase de la secuencia de mecanizado. Este último modelo define la geometría por conseguir en cada operación.
La definición de esta geometría hace que el proceso de mecanizado de tres fases sea diferente de la progresión típica de “desbaste, semiacabado, acabado”. Por ejemplo, el “desbaste” de la fase uno todavía tiene como objetivo maximizar la eliminación de material, pero el objetivo es más ambicioso que lograr una aproximación cercana a la forma final de la pieza. Más bien, la pieza de trabajo debe coincidir de manera precisa con el modelo 3D que la define. Cuándo y dónde dejar material adicional en ese modelo depende de qué partes del diseño aún estén en desarrollo y deben estar “protegidas” cuando comience el mecanizado.
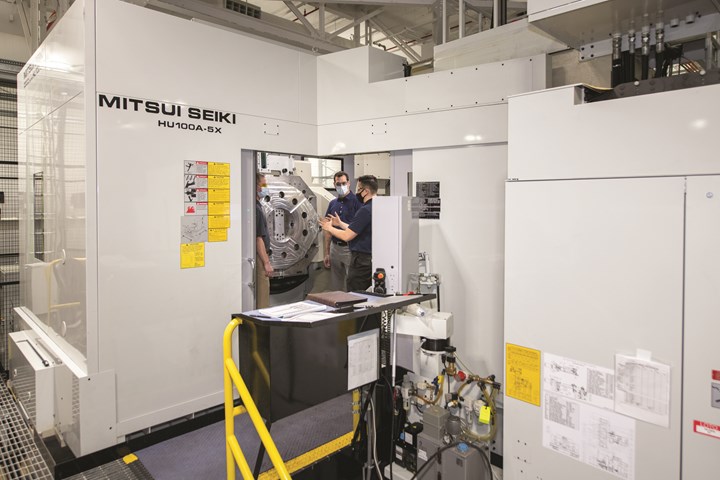
El equipo de ingeniería revisa el progreso del mecanizado de una cubierta de ramal. Cada uno de los HMC gemelos de cinco ejes de la celda tiene una mesa cuadrada de 1,000 mm (39.4 pulg.), un recorrido en el eje X de 1,300 mm (51.2 pulg.) y 1,000 mm (39.4 pulg.) de recorrido para los ejes Y y Z. El husillo, con una interfaz de portaherramientas personalizada de doble contacto, tiene una potencia nominal de 37 Kw (50 hp).
Esta estrategia permite configurar toda la infraestructura de fabricación necesaria, incluidos los programas NC, las herramientas de corte y los accesorios, semanas antes de que finalicen los diseños, en lugar de semanas después. Mientras tanto, los programadores pueden comenzar a optimizar la siguiente fase del mecanizado. Por ejemplo, los modelos 3D de la caja reductora mecanizada de la fase uno ayudaron a refinar y validar la precisión del mecanizado de la fase dos en aproximadamente 48 % menos de tiempo que proyectos similares en el pasado, dice Patry. Entre otras oportunidades, los programadores descubrieron que ciertos dispositivos de fijación de la fase uno podrían usarse nuevamente.
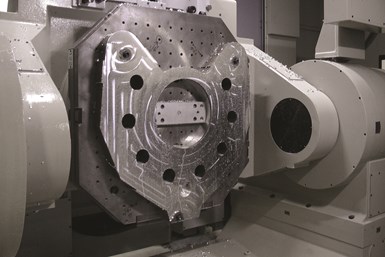
Una inspección genera un “mapa de calor” para validar la precisión del proceso de remoción de metal antes de que esta cubierta de derivación pase a la siguiente operación de mecanizado.
En cada fase, los mapas de calor codificados por colores de la pieza de trabajo facilitan la detección de las discrepancias entre los modelos de piezas mecanizadas y los modelos de control derivados de la simulación. Los tonos de rojo y naranja indican la presencia de material fuera de la banda de tolerancia, quizás debido a la desviación de la herramienta, fuerzas de sujeción o tensiones residuales del material. Si es necesario, investigar y corregir las causas fundamentales de estas discrepancias evita que las piezas pasen a la siguiente etapa, hasta que la pieza de trabajo coincida con el modelo de ingeniería. Al mismo tiempo, el proceso digital se puede actualizar para reflejar el rendimiento del mundo real. Por ejemplo, la desviación de la herramienta se puede cuantificar y almacenar para futuras simulaciones.
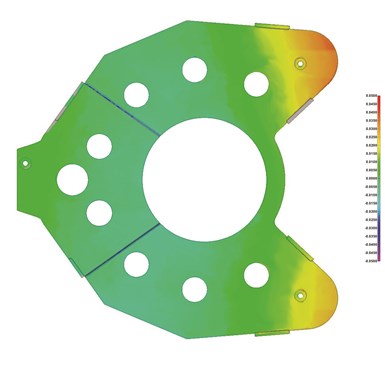
Este enfoque iterativo elimina las piezas defectuosas y el retrabajo. En el proceso, conduce a reducciones significativas en el tiempo de entrega porque la primera pieza mecanizada se puede enviar directamente al ensamblaje (o para prueba). La caja reductora principal producida en el HMC es un buen ejemplo. El mecanizado de la primera pieza comenzó en julio de 2020, aproximadamente 10 semanas antes de que finalizara el trabajo de diseño de esa pieza.
“No solo se produce la primera pieza más rápido, sino que también esa pieza es un activo utilizable —dice Patry—. En el enfoque anterior, planificaríamos considerando que solo se pueda utilizar la segunda pieza producida, y esa segunda pieza podría producirse tres o cuatro meses después de la primera”.
En resumen, decir “cortamos antes de cortar” en esta fábrica es claramente sensato y preciso.
Prueba de concepto de la celda de mecanizado
El éxito de esta celda de mecanizado es la culminación del concepto de fábrica digital de Sikorsky, dice Patry. “Consideramos que es una prueba de que nuestro marco de fábrica inteligente y nuestro entorno basado en modelos digitales son sólidos y altamente efectivos. El Raider X es un ganador porque la fábrica que lo construye es una ganadora”.
El marco de fábrica inteligente de Sikorsky les permite a los diseñadores de productos, planificadores de procesos, programadores de piezas y gerentes de todos los departamentos de fabricación trabajar juntos en un entorno digital común y unificado. Las ventajas de trabajar dentro de este marco de fábrica inteligente se reflejan en las actividades tras bambalinas, que conducen al corte de viruta en la celda de mecanizado.
El núcleo del entorno de fabricación digital en el que se desarrolla el Raider X es el software de diseño y fabricación Dassault 3DX. Este es el repositorio del diseño virtual del Raider X, con un modelo 3D de cada componente de la aeronave. Patry se refiere a esta base de datos integrada como una “fuente única de verdad” para todo el equipo del programa, y se actualiza y refina constantemente con información relevante.
Las simulaciones y los gemelos digitales le permitieron a la empresa diseñar y configurar un hangar para ensamblar el Raider X mucho antes de que llegaran los primeros fuselajes.
Los componentes que se van a mecanizar se pueden trabajar en el entorno de gemelos digitales como prototipos virtuales en torno a los cuales se desarrollan los procesos del taller.
La simulación de estos procesos implica modelos 3D de todo el proceso, incluidas representaciones exactas de las estructuras de la máquina y su cinemática para replicar cómo responde una herramienta de corte a los servocomandos. El caso es el mismo para los conjuntos de herramientas de corte, incluida la geometría de todos los insertos, cuerpos de herramientas y portaherramientas.
“Estos datos se definen en los modelos 3D y crean un hilo continuo desde el programa NC hasta la configuración física de la herramienta de corte y el controlador de la máquina —dice Patry—. Estos puntos de datos críticos se verifican y validan automáticamente antes de que la máquina comience a usar esa herramienta de corte”.
Todos estos modelos 3D se unen en el software de simulación Vericut para crear escenarios de mecanizado virtual que los programadores utilizan para optimizar el proceso. En última instancia, los resultados de las simulaciones se incorporan a los modelos virtuales que definen cómo debe verse la pieza en las diferentes etapas del mecanizado.
La posibilidad de que múltiples programadores trabajen en la misma pieza en diferentes etapas también reduce el tiempo de entrega. “Solíamos tener un programador de NC trabajando en una pieza completa, por lo que se producían retrasos entre las operaciones —explica Patry—. Al trabajar en tres fases de mecanizado distintas, podemos asignar un programador NC a cada fase, porque tenemos un modelo virtual para cada fase. Más personas pueden actuar al mismo tiempo”.
Más allá del mecanizado
La celda de mecanizado se mejorará con capacidades adicionales, que podrían incluir robótica u otra automatización, a medida que estén disponibles. Su construcción sigue un enfoque de “bloques de construcción” que facilita la integración de más máquinas o la duplicación, ya sea en Lockheed Martin o en las instalaciones de un proveedor. La celda también sirve como prototipo conceptual para celdas de mecanizado adicionales en la fábrica digital de Sikorsky. Aunque estas celdas difieren de la celda Mitsui/G&L en muchos aspectos, incorporarán y ampliarán capacidades digitales ya probadas.
Los mismos conceptos y capacidades también funcionan más allá del mecanizado CNC. Otras celdas ya están en funcionamiento para la construcción de piezas compuestas, la producción y el ensamblaje de engranajes, y todas comparten la misma filosofía de conectividad e integración digital.
De hecho, las simulaciones y los gemelos digitales le permitieron a la empresa diseñar y configurar un hangar para ensamblar el Raider X mucho antes de que llegaran los primeros fuselajes. Además de los métodos de ensamblaje, las técnicas para transportar piezas y verificar el cumplimiento de los pasos de ensamblaje ya se habían optimizado para lograr eficiencia y seguridad en el espacio virtual.
En muchos casos, el uso de la realidad aumentada en 3D reveló problemas que podrían abordarse fácilmente en las etapas de planificación. Quizás era necesario ampliar un pasillo o simplificar el ajuste de la altura en una plataforma de trabajo para el alcance o la comodidad del ensamblador. “Esta simulación fue una herramienta muy poderosa, que le permitió a todo el equipo ver cómo se iba a construir la aeronave, todo durante la fase de diseño conceptual”, dice Germanowski.
Patry reconoce que Sikorsky ha desarrollado una serie de innovaciones patentadas que mejoraron significativamente la forma en que su marco de fábrica inteligente mejora el rendimiento de la máquina en el taller.
Como ejemplo, cita nuevas formas de descargar y actualizar datos esenciales relacionados con los parámetros de mecanizado. Y, sin embargo, enfatiza que el factor más importante en el éxito no ha sido ninguna “fórmula secreta”. Más bien, es el hecho de que todos han adoptado y abrazado un enfoque digital que les permite colaborar de manera más efectiva y, por extensión, hacer que “cortamos antes de cortar” sea una realidad.
En Sikorsky, la manufactura digital se ve como un esfuerzo de equipo que involucra a todos, desde los ingenieros de diseño y fabricación hasta el personal de operaciones y los gerentes de las instalaciones.
CONTENIDO RELACIONADO
-
Los beneficios de las máquinas-herramienta multitarea
La tecnología de máquinas-herramienta multitarea ha revolucionado la manufactura y sigue desempeñando un papel fundamental en talleres de mecanizado que han adoptado esta tecnología.
-
Maquinado en cinco ejes revoluciona el diseño y la manufactura
Además de solucionar los retos que trae el mecanizado de geometrías complejas, los nuevos centros de maquinado en cinco ejes integran capacidades de fresado, torneado, manufactura aditiva y láser, junto con las tecnologías propias de la Industria 4.0.
-
¿Por qué usar torno-fresado?
Los fabricantes de máquinas-herramienta se dieron cuenta de que las piezas torneadas a menudo requerían también, al menos, algún trabajo de fresado o taladrado. Por ello aumentaron las capacidades de los tornos mediante husillos adicionales para el trabajo con herramientas giratorias. De esa manera surgieron las máquinas de torno-fresado.