Enfocarse en el rendimiento empodera a las personas y las máquinas
Las lecciones aprendidas en las máquinas de medición por coordenadas (CMM) con supervisión de robots se traducen en un proceso de mecanizado multitarea con autocorrección.
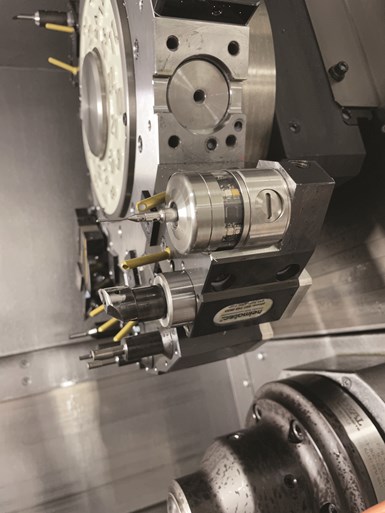
En Lowell Inc., las sondas en la máquina son poderosas herramientas de automatización. Fotos Peter Zelinski.
Para cualquier persona interesada en el mecanizado de dispositivos médicos, vale la pena visitar Lowell Inc., equipada con una amplia variedad de equipos de corte multihusillo, multieje y multifuncionales. Dada la amplia y altamente avanzada tecnología en el taller, es probable que cualquier visitante también se sorprenda al saber que más de la mitad de los ingresos de la empresa y casi la mitad de sus piezas provienen de solo seis de las 60 máquinas-herramienta con que cuenta en total.
¿Cómo se puede hacer esto? “Hemos eliminado la mayor cantidad posible de información humana del proceso”, dice Jim Stertz, quien manejó este grupo de máquinas hasta su reciente jubilación.
Contenido destacado
Ahora la fabricación es controlada por sondas y programación, explica Stertz. Cada máquina tiene dos sondas Renishaw montadas en la torreta, una para el husillo principal y otra para el husillo secundario. Estas sondas, que se usan ampliamente, interrumpen de manera rutinaria el corte para enviar datos al CNC y realizar así correcciones automáticas durante el proceso. Incluso en volúmenes de 400 a 1,200 piezas por mes, un tiempo de ciclo más largo es un pequeño precio para evitar el desperdicio y reducir el trabajo adicional posterior para el sistema de control de calidad, dice. El desempeño es lo primero.
Gracias a la disminución resultante del 80 % en las horas de mano de obra por pieza, tres funcionarios pueden mantener las seis máquinas en funcionamiento las 24 horas del día, los 7 días de la semana sin emplear mucho más que un solo turno en sitio, dice Stertz. La automatización puede ser igual de útil durante los periodos de menor ocupación, agrega, porque flexibilizar los cronogramas de producción con la demanda es más fácil con menos personas.
La automatización de desarrollo local de este fabricante de equipo médico de Minneapolis es notable porque cubre no solo el movimiento físico de la medición, sino también la consecuente toma de decisiones. De hecho, el ejemplo de Lowell sugiere que esta podría ser la forma de automatización más poderosa. También podría ser más barato. En este caso, la HMI personalizada, que permite el monitoreo remoto e incluso el control del proceso, se construyó sobre poco más que la red de máquinas preexistente, y componentes estándar relativamente económicos.
Esto no quiere decir que la implementación fuera fácil. Sin embargo, el equipo tenía la ventaja de la experiencia anterior, particularmente de un proyecto de automatización en el departamento de control de calidad. Cuando los ciclos de retroalimentación comenzaron a tomar forma, ya se habían aprendido lecciones sobre la prioridad que se le debe dar al desempeño (incluso a expensas del tiempo de inactividad). Igual de importante, el proyecto anterior ya había demostrado el valor de centrarse no solo en la reducción de la mano de obra, sino también en la creación de oportunidades para empoderar a las personas.
Una mentalidad que pone la calidad primero
El primer proyecto de automatización comenzó en 2008, cuando Stertz dirigía el departamento de control de calidad. El taller acababa de agregar una segunda máquina de medición por coordenadas (CMM) para complementar la máquina existente y había construido un laboratorio climatizado de 450 pies cuadrados para albergar ambas.
La nueva máquina funcionó sin problemas tras dedicar meses de trabajo a las optimizaciones de programación, como permitir que la CMM escaneara una pieza y cargara automáticamente la rutina de medición programada. Sin embargo, el personal no podía cargar y descargar piezas lo suficientemente rápido para mantenerse al día con las máquinas. Las CMM a menudo permanecían inmóviles, para gran frustración de los clientes y los operarios del taller, que esperaban los resultados de la inspección.
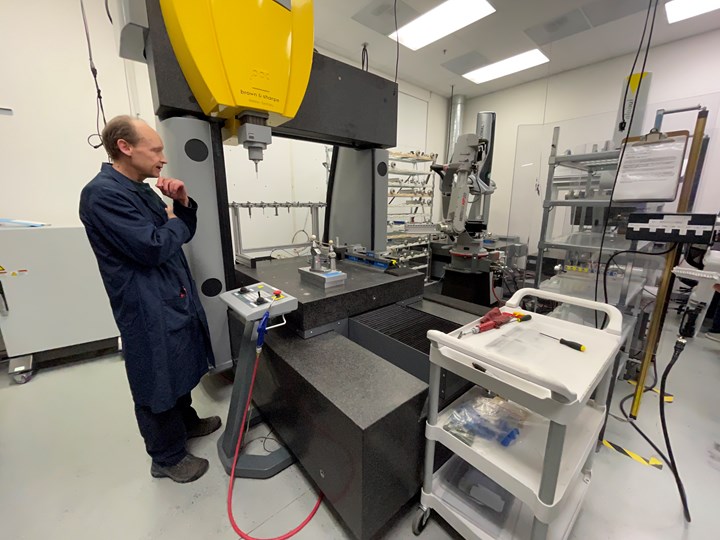
Jim Stertz, quien se jubiló a principios de este año, pasó a la planta de producción luego del éxito de la automatización en el departamento de control de calidad. El brazo robótico Motoman HP20 ahora trabaja con tres CMM (una Brown & Sharpe Global S CMM, una Brown & Sharpe Global Advantage y una Leitz PMM-C 700, de Hexagon Manufacturing Intelligence).
Concebir y configurar el sistema que desbloquearía la capacidad total de las CMM tomó 18 meses adicionales de trabajo, en gran medida por parte de Stertz y del actual gerente del departamento, Brad Traczyk. En la actualidad, Traczyk supervisa esencialmente el mismo proceso, en el que las piezas se colocan previamente en pallets y se les asigna una prioridad numerada.
Este número determina la forma en que un robot de seis ejes carga los pallets en un segundo estante de almacenamiento para su eventual transferencia a una de las tres CMM, según el principio de “el primero que entra es el primero que sale”. Organizar el trabajo un viernes para realizar inspecciones sin supervisión durante un fin de semana durante los periodos de mucho trabajo, a menudo puede llevar las tasas de ejecución semanales a 150 horas o más.
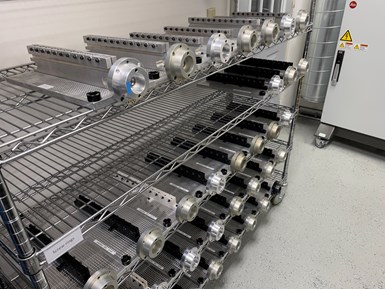
El proceso en torno al robot se desarrolló de forma interna por completo, desde la activación hasta la programación, la fijación estandarizada y dos bastidores de escenario, uno de los cuales se puede ver aquí.
Stertz dice que esta automatización es crítica hoy por la misma razón que lo fue en 2008: los clientes continúan requiriendo precisión adicional y las respectivas pruebas adicionales. Los implantes para el corazón y la columna, generalmente, son complejos, diminutos y se producen en grandes volúmenes con materiales costosos como el titanio y aleaciones cromo-cobalto. Ya sea en la sala de las CMM o en el taller, las mediciones durante el proceso son comunes para evitar el costo directo del desperdicio, así como las diversas obstrucciones de flujo parcial que un defecto no descubierto podría crear aguas abajo. Los robots, los pallets y un medio que permite una forma fácil de priorizar dinámicamente el trabajo, ayudan a gestionar las inspecciones finales y el trabajo de evitar que las máquinas produzcan piezas no conformes.
El rendimiento se impone sobre el tiempo de ciclo
Stertz reconoció una importante oportunidad para replicar su éxito en automatización en el taller con un trabajo en particular: el ensamblaje para un implante cardíaco que consta de 12 números de piezas de alto volumen. Repetir la producción de este número manejable de piezas brindaría una previsibilidad más que suficiente para justificar la optimización de un proceso en torno a este trabajo, fue su razonamiento.
El trabajo, que ya se encontraba entre los contratos más importantes de la empresa, también prometía ampliar los volúmenes e iteraciones regulares del diseño, si la empresa podía mantenerse al día sin comprometer los estrictos estándares de calidad.
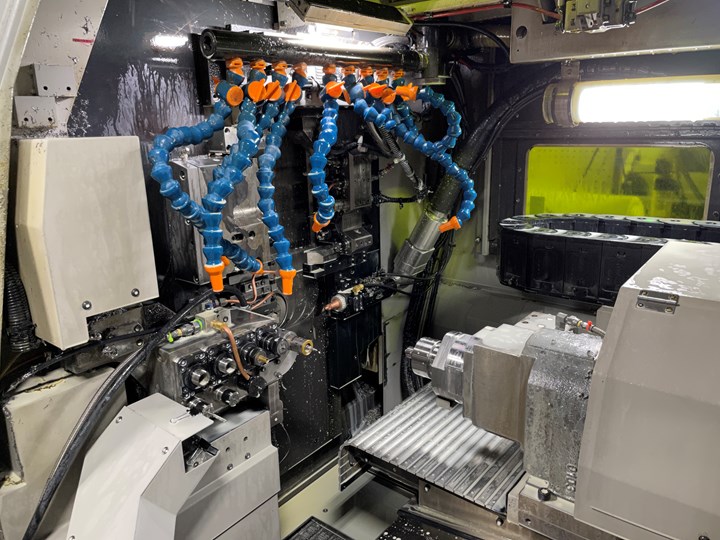
Una vista de la zona de trabajo del nuevo Tsugami SS327-5AX, de Lowell, que agrega corte por láser a la ya variada capacidad de un torno tipo suizo.
Un proceso de mecanizado eficiente ha ayudado, particularmente cuando se ve impulsado por la inversión continua en nueva tecnología. Por ejemplo, la más nueva de las seis máquinas que procesan el ensamblaje del implante cardíaco es un torno tipo suizo Tsugami SS327-5AX. Además de los cinco ejes, las múltiples funcionalidades y la estabilidad de corte reforzada por bujes guía, la máquina cuenta con un cabezal de corte por láser integrado, ideal en piezas demasiado sensibles para la presión de una herramienta de corte.
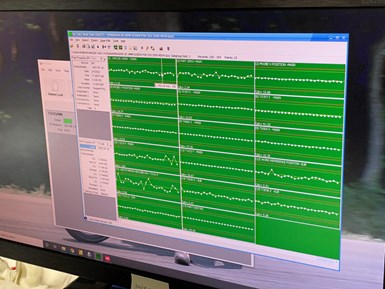
Esta pantalla se actualiza casi en tiempo real a medida que las lecturas de la sonda se comparan con los umbrales definidos por el usuario.
Sin embargo, Stertz considera que el sondeo sobre la máquina es la capacidad más poderosa de las seis máquinas multitarea. El valor del sondeo sobre la máquina no está en reducir el tiempo de corte, sino en reducir la métrica que importa: el costo de mano de obra por pieza (que, como se mencionó, ha disminuido en un 80 %). Cada operación crítica es monitoreada. Dependiendo de dónde se encuentre la lectura dentro de los umbrales definidos por el usuario, la devolución de los datos al CNC desencadena una de tres acciones: seguir cortando; detener el eje y enviar una notificación automática, o ajustar la compensación de la herramienta para equilibrar una operación que se desvía demasiado cerca del límite de la banda de tolerancia (ya sea debido al desgaste de la herramienta o a la desviación en el husillo o la torreta).
Este sondeo de corrección de procesos puede agregar minutos a los tiempos de ciclo en los que los segundos importan, al menos en términos de rendimiento de cualquier máquina. Esto está bien por la misma razón por la que estaba bien comprar un robot para el departamento de control de calidad, solo para dejarlo inactivo durante largas rutinas de inspección: el desempeño general es lo más importante.
En ese sentido, ambos proyectos de automatización proporcionaron el mismo beneficio. Stertz atribuye flujos de trabajo más fluidos a una mayor confianza en la calidad de las piezas; menos inspecciones CMM en menos operaciones de la pieza, y menos clasificación, reelaboración y desechos. Quizás lo más significativo sea que ambos sistemas de automatización liberaron a las personas para realizar tareas de mayor valor.
Los verdaderos ganadores
El compromiso de Lowell con el sondeo sobre la máquina es extremo. Tolerancias más estrictas (algunas que van hasta +/- 0.00005”) pueden inspirar cortes “fantasmas”: pasadas tomadas después de un ajuste de compensación que no eliminan más material que la cantidad de compensación. El sistema prueba de nuevo y, potencialmente, refina el desplazamiento para reducir la probabilidad de empujar una operación de la pieza fuera de los límites de conformidad.
Sin la automatización, es decir, al depender por completo de herramientas manuales y la entrada manual de datos, un empleado tendría que “inspeccionar la operación correcta en el momento adecuado, y luego tomar una decisión sobre qué hacer, y después hacer la compensación correcta en el lugar correcto en la página de compensación del control de la máquina”, dice Stertz.
No todos pueden hacer esto. En especial, aquellos que probablemente puedan tener mejores cosas que hacer, es decir, escribir programas para las máquinas. El caso fue similar para el robot, que liberó al personal de control de calidad para escribir programas para las MMC. El robot puede permanecer inactivo durante una gran parte del tiempo, pero ese es el punto. No se cansa; no comete errores, y está “siempre ahí, listo cuando se necesita —dice Stertz—. Permite que más funcionarios atiendan el proceso de manera efectiva. Hay menos decisiones que tomar”.
Empoderar a las personas no es solo el resultado de la automatización. También es la génesis de la automatización.
La HMI personalizada, de Lowell, también ayuda a las personas a aprovechar al máximo su tiempo. De cosecha propia, esta interfaz proporciona gráficos de control de procesos estadísticos (SPC) y otras pantallas a las que se puede acceder desde un teléfono móvil. Cuando se le preguntó la razón para que Lowell desarrollara su propio sistema de monitoreo y alertas remotas, Stertz menciona una característica adicional en particular, que los desarrolladores por lo general evitan: el control remoto, que ha demostrado ser particularmente útil en casos en que los husillos se detienen debido a una falsa alarma.
Por ejemplo, una máquina detenida debido a una condición de alarma puede requerir solo un simple soplado de virutas y un reinicio del ciclo. Una vez verificado con la ayuda del sistema de cámara Google Nest en la zona de trabajo de la máquina, este problema se puede solucionar (y reiniciar el ciclo) de forma remota para evitar un retraso costoso.
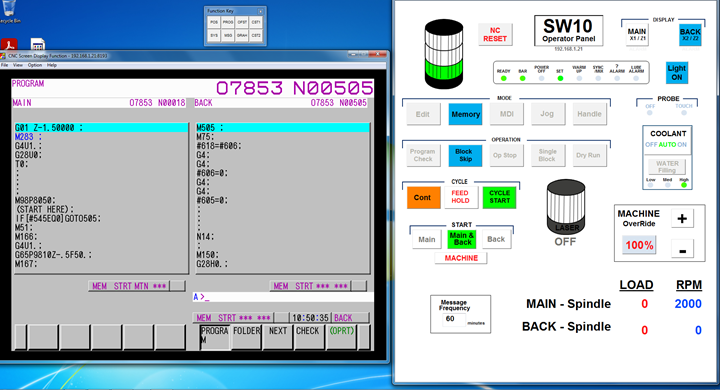
Una interfaz personalizada proporciona monitoreo y control remoto de las máquinas-herramienta.
La relativa simplicidad del sistema también es atractiva, dice Stertz. Se ejecuta en un dispositivo de extremo: una computadora industrial simple que se vincula con el control de cada máquina directamente a través de su dirección IP en la red interna del taller. Sacando su teléfono de su abrigo, revela un panel de operador con retención de alimentación, anulación rápida y otros controles, además de representaciones gráficas de los resultados de la sonda actualizados casi en tiempo real y, por supuesto, la alimentación de la cámara y las notificaciones de alarma/parada. Los dispositivos inteligentes también pueden acceder al programa de la máquina para editarlo o simplemente colocar el cursor para reiniciar el programa.
Creando oportunidades
La idea de que la automatización empodere a las personas no es nueva, pero la historia de Lowell agrega otra capa. El éxito con la automatización es un testimonio no solo de la habilidad y dedicación de Stertz, sino también del equipo de colaboradores que reunió para ayudarle, muchos de los cuales comenzaron a trabajar en el sistema como empleados sin experiencia de una escuela técnica local. Estos empleados hicieron una contribución enorme, dice Stertz. “Ellos adelantaron todo el trabajo, solo les dimos la oportunidad”.
En otras palabras, empoderar a las personas no es solo el resultado de la automatización. También es la génesis de la automatización. Los sistemas implementados en Lowell existen porque alguien no solo estaba dispuesto a invertir el tiempo y los fondos, sino también a escuchar ideas no convencionales.
Crear oportunidades para que las personas hagan su mejor trabajo significa liberarlas de las tareas mundanas, y también de barreras para la experimentación y el aprendizaje e, incluso, del miedo a cometer errores. Así, las personas se vuelven verdaderamente libres para desarrollar circuitos de retroalimentación u otras variedades de automatización que pueden asegurar un futuro brillante para una empresa como Lowell Inc.
CONTENIDO RELACIONADO
-
Los 10 países más automatizados del mundo, según la IFR
La densidad promedio de robots industriales en la industria manufacturera mundial alcanzó un récord mundial de 113 unidades por cada 10,000 empleados. Conozca cuáles son los países que lideran la carrera hacia la automatización.
-
Revolucionando las rutinas del taller metalmecánico: 5 aplicaciones CNC
Descubra 5 aplicaciones CNC que están transformando el funcionamiento de los talleres de mecanizado, impulsando la eficiencia y mejorando la precisión.
-
Guía para implementar un robot colaborativo en sus máquinas CNC
En tiempos de distanciamiento social, nada mejor que analizar el flujo de operaciones en su taller y determinar en qué áreas la automatización es el camino para elevar su productividad y reasignar tareas operativas. El uso de robots colaborativos puede significar un importante atajo.